Turn-Milling Compound Machining Center refers to the place where lathe and milling machine are processed together. It is an advanced cutting processing method that uses the combined motion of milling cutter rotation and workpiece rotation to realize the cutting processing of the workpiece, so that the workpiece can meet the requirements in terms of shape accuracy, position accuracy, and processed surface integrity.
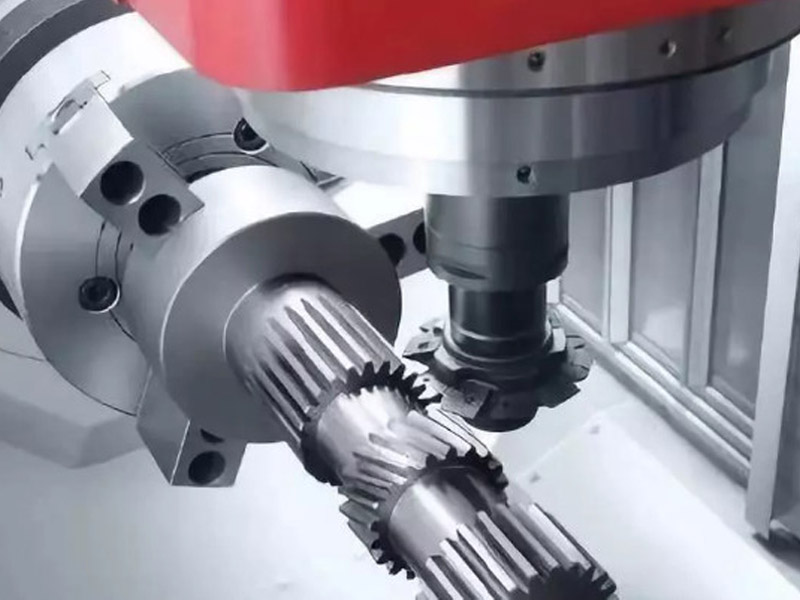
Compared with conventional CNC machining technology, the outstanding advantages of Turning-Milling-Compound-Machining-Center are mainly reflected in the following aspects:
(1) Shorten the product manufacturing process chain and improve production efficiency.
A variety of special tools and new tool arrangements can be installed to reduce tool change time and improve processing efficiency. Turning and milling composite processing can complete all or most of the processing operations in one clamping, thereby greatly shortening the product manufacturing process chain. In this way, on the one hand, the production assistance time caused by the change of the mounting card is reduced, and at the same time, the manufacturing cycle and the waiting time of the tooling fixture are reduced, which can significantly improve the production efficiency.
(2) Reduce the number of clamping times and improve machining accuracy.
The reduction of the number of card installations avoids the accumulation of errors caused by the transformation of the positioning reference. At the same time, most of the turning and milling processing equipment has the function of online detection, which can realize the in-situ detection and precision control of key data in the manufacturing process, thereby improving the processing accuracy of the product; the high-strength integrated bed design improves the difficulty of cutting difficult materials Gravity processing capacity; the machine is equipped with an automatic feeding device, which can realize automatic feeding to continuous, basically realize the assembly line operation of a single machine.
(3) Save floor space and production costs.
Compact and beautiful appearance design, improved space utilization, more convenient for maintenance and repair to maximize customer satisfaction; although the single unit price of the turning and milling compound processing equipment is relatively high, but due to the shortening of the manufacturing process chain and the reduction of equipment required for the product , And the reduction of the number of fixtures, workshop floor space and equipment maintenance costs can effectively reduce the overall fixed asset investment, production operation and management costs
Contact us for Turn-Milling related products and services, such as precision stainless steel components. Custom cnc aluminum parts.
评论
发表评论