JY Machinery offers high-quality precision and cost-effective CNC machining services for custom titanium parts to enhance manufacturing efficiency.
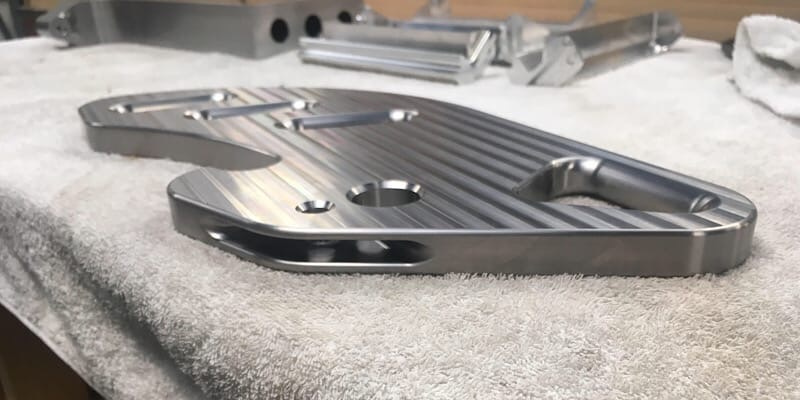
Custom Titanium alloy manufacturing is mainly used for the production of aircraft engine compressor components, followed by the structural parts of rockets, missiles and high-speed aircraft, and related medical accessories. The density of titanium alloy is generally about 4.51g/cm3, which is only 60% of steel. The density of pure titanium is close to that of ordinary steel. Some high-strength titanium alloys exceed the strength of many alloy structural steels. Therefore, the specific strength (strength/density) of titanium alloy is much greater than other metal structural materials, and parts with high unit strength, good rigidity and light weight can be produced. The aircraft's engine components, skeleton, skin, fasteners and landing gear all use titanium alloys.
The Reasons Why Titanium Is Hard to Machine
If you want to process custom titanium alloys parts, you must have a thorough understanding of its processing mechanism and phenomena. Many processing parties believe that titanium alloy is an extremely difficult material to process because of insufficient understanding of it. Today JY Machinery will analyze the processing mechanism and phenomenon of titanium alloys for everyone.
1)The first thing to talk about is the physical phenomenon of titanium alloy processing. Although the cutting force during processing of titanium alloy is only slightly higher than that of steel of the same hardness, the physical phenomenon of processing titanium alloy is much more complicated than that of processing steel, which makes the difficulty of titanium alloy processing rise linearly.
2)The thermal conductivity of most titanium alloys is very low, only 1/7 that of steel and 1/16 that of aluminum. Therefore, the heat generated in the process of cutting titanium alloy will not be quickly transferred to the workpiece or taken away by the chips, but will be concentrated in the cutting area, and the temperature generated can be as high as 1,000 ℃ or more, causing the cutting edge of the tool to quickly wear, crack and Generate built-up edge, wear blades quickly appear, and generate more heat in the cutting area, further shortening the life of the tool.
3)The high temperature generated during the cutting process also destroys the surface integrity of the titanium alloy parts, resulting in a decrease in the geometric accuracy of the parts and a work hardening phenomenon that severely reduces its fatigue strength.
4)The elasticity of titanium alloy may be beneficial to the performance of parts, but in the cutting process, the elastic deformation of the workpiece is an important cause of vibration. The cutting pressure causes the "elastic" workpiece to leave the tool and rebound, so that the friction between the tool and the workpiece is greater than the cutting action. The friction process also generates heat, which aggravates the poor thermal conductivity of titanium alloys.
5)This problem becomes even more serious when processing thin-walled or ring-shaped parts that are easily deformed. It is not an easy task to process thin-walled titanium alloy parts to the expected dimensional accuracy. Because when the workpiece material is pushed away by the tool, the local deformation of the thin wall has exceeded the elastic range and plastic deformation occurs, and the material strength and hardness of the cutting point increase significantly. At this time, machining according to the originally determined cutting speed becomes too high, which further leads to sharp tool wear. It can be said that "heat" is the "root disease" that causes the difficulty of titanium alloy processing.
The Useful Tips for titanium alloy parts machining
As one of leader in the CNC industry, JY Machinery has carefully sorted out a process know-how for titanium alloys parts machining, and encourages the entire industry. We stated that on the basis of understanding the processing mechanism of titanium alloys, plus previous experience, the main process know-how for processing titanium alloys is as follows:(1) Use positive-angle geometry inserts to reduce cutting force, cutting heat and workpiece deformation.
(2) Maintain a constant feed to avoid hardening of the workpiece. The tool must always be in the feed state during the cutting process. The radial tool engagement ae during milling should be 30% of the radius.
(3) Use high-pressure and large-flow cutting fluid to ensure the thermal stability of the machining process and prevent surface degeneration and tool damage due to excessive temperature.
(4) Keep the cutting edge of the blade sharp. Blunt tools are the cause of heat build-up and wear, which can easily lead to tool failure.
(5) Processing in the softest state of the titanium alloy as much as possible, because the material becomes more difficult to process after hardening, heat treatment increases the strength of the material and increases the wear of the blade.
(6) Use a large arc radius or chamfer to cut in, and put as many cutting edges as possible into the cutting. This can reduce the cutting force and heat at every point and prevent local damage. When milling titanium alloys, among the cutting parameters, the cutting speed has the greatest influence on the tool life, followed by the radial tool engagement (milling depth).
When the hardness of titanium alloy is greater than HB350, cutting is particularly difficult, and when the hardness is less than HB300, it is prone to sticking and cutting is difficult. Therefore, the problem of titanium alloy part machining can be solved from the blade. The blade groove wear during titanium alloy processing is the local wear of the back and front along the depth of cut, which is often caused by the hardened layer left by the previous processing. The chemical reaction and diffusion of the tool and the workpiece material at a processing temperature of over 800°C are also one of the reasons for the formation of groove wear. Because during the machining process, the titanium molecules of the workpiece accumulate in the front area of the blade and are "welded" to the blade under high pressure and high temperature, forming a built-up edge. When the built-up edge is peeled from the blade, it will take away the carbide coating of the blade. Therefore, titanium alloy processing requires special blade material and geometry.
Get your custom titanium alloy project started today
When you send out 3D CAD documents to us, JY Machinery will provide you with instant price, on-demand delivery time, as well as design for manufacturability comments for your customized CNC machining components on materials and also producing process, to make sure that the component can meet your expectations as well as budget plan demands.
评论
发表评论