Precision hand surface grinding machine
1. Basic knowledge of grinding- Type, characteristics and process of grinding
- Abrasive and abrasive tools
- Grinding fluid
- Safety protection
- Common grinders and auxiliary equipment of grinders (introduction and application methods of grinders and other auxiliary equipment of grinders, including flat clamp, inclinometer, sine table, sine gauge, arc perspective dresser, punch molding machine, punch grinding machine and various self-made tools and equipment);
- Balancing and dressing of grinding wheel
- Matters needing attention before processing (should include safety knowledge, machine tool maintenance, work specification, dressing of platform and plate)
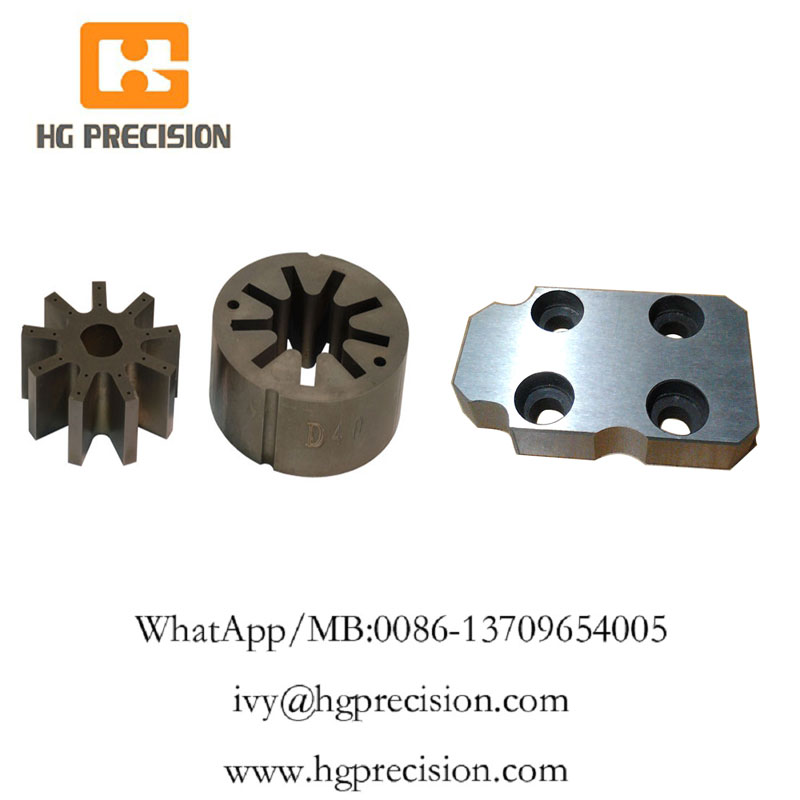
2.Plane (should include all kinds of material processing and grinding wheel selection rules, such as aluminum, brass, copper, all kinds of mold steel, white steel and so on.And grinding flakes for deformation)
3.Right Angles
4.Groove cutting (should include selection, dressing, tool setting and other matters needing attention of grinding wheel)
5.Inclination (should include a brief introduction to trigonometric functions and a scientific calculator explanation of inverse trigonometric calculation)
6.Arcs (shall include the method of repairing arcs with the perspective arc dresser and punch shaper)
7.Inclination Arc (including the principle and formula derivation of various inclination arc)
8.Chapter
9.compound slope
10.Other processing (mainly including various special workpiece processing methods, such as head round body square, oval, punch, various shaped workpiece, etc.)11. Items to be completed after Molding (full inspection of dimensions, various inspection methods and handover)
评论
发表评论