1. Overview of CNC Machining
Based on the development of a milling machine automatic processing equipment, the two processing technology is basically the same, the structure is similar.CNC milling machine with cutter base is called machining center.
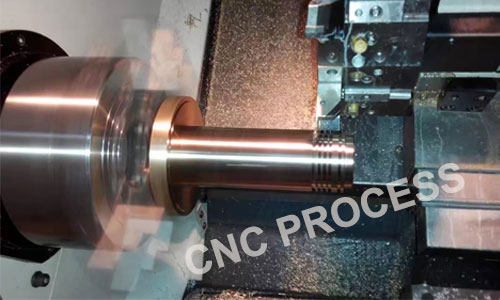
2. The scope of function of CNC Machining
Good adaptability and flexibility in processing, and can process parts with particularly complex contour shape or difficult to control size.High processing precision, stable and reliable processing quality, numerical control device pulse equivalent is generally 0.001mm, high precision numerical control system can be up to 0.5 m, numerical control processing also avoid operator error.Production automation degree is high, can reduce the labor intensity of the operator.Conducive to production management automation.3. Classification of CNC Processing in the factory
There are two kinds of CNC in the factory:
- Ordinary CNC: less than 8000 RPM, can be a large tool, suitable for milling, drilling, boring, flying material and other type tolerance accuracy of more than 0.02 forming processing.
- High-speed CNC: milling processing with surface roughness above Ra0.4 and profile tolerance accuracy above 0.005.
CNC is suitable for tungsten steel milling cutter, the surface needs coating, according to the work piece hardness selection.
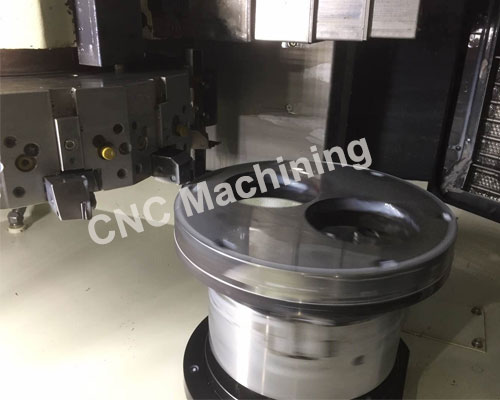
4. Constraint relationship
1) The depth of the machining hole is proportional to the diameter of the knife.2) It is difficult to ensure high perpendicularity in hard material processing.
3) Tool wear has a direct impact on the size of the work piece.
5. Relationship with process engineering
Select the appropriate type of machine according to the parts.
评论
发表评论